2005 Brampton Engineering 3" extruder with screenchanger
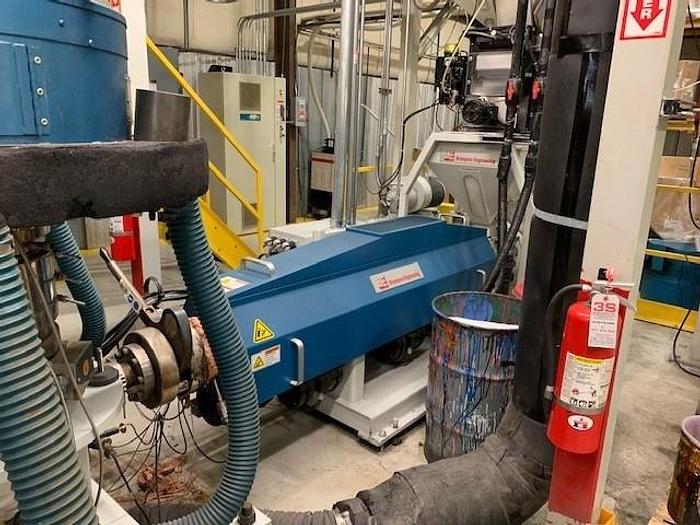
2005 Brampton Engineering 3" extruder with screenchanger
Description
ONE BE SINGLE SCREW EXTRUDER PACKAGE
Brampton Engineering heavy duty extruders combine the rugged design needed to run under full load for 24 hours a day with the flexibility to run a wide range of polymers. An extruder is an integrated system combining many components:
Extruder Screw:
- since it is the key component, we custom engineer each screw to provide optimum processing characteristics
- each screw includes Colmonoy 83 hard-facing on the flights for long wear, chromium plating in the root for ease of cleaning and one or more mixing sections to ensure thorough mixing
- a barrier melt channel screw will be provided
The extruder barrel includes:
- a continuous Xaloy 800 bimetallic liner extending from the feed section to the end of the barrel, eliminating the uneven wear and hang-up points common to other designs
- pressure transducer mounting in the end of the barrel
- breaker plate of non-reversible design, if a screen changer is not supplied
- threaded discharge end for connection to downstream equipment
The feed throat and hopper include:
- cast iron feed throat with machined surfaces for precise alignment
- tangential feed to ensure even flow into the screw feed section
- feed throat cored for water cooling for optimum temperature control
- large capacity hopper constructed with heavy gauge sheet metal including a sight glass, slide gate shutoff and material dumping chute
The drive system includes:
- AC Vector fully programmable digital drive and motor with 0.1% speed regulation over 100:1 speed range, diagnostic capability. Network card can be added if required. Line reactor included to reduce line noise
- heavy duty double reduction gearbox transfers power effectively and smoothly to the screw, has an integral thrust bearing for precise alignment
Temperature control of the polymer is achieved with an air cooled heating system that includes:
- deep finned aluminum heaters which respond quickly to changes in temperature
- high capacity blowers direct cooling air uniformly around the heaters for maximum heat removal
- insulated aluminum shroud surrounds the heater to keep heat in and direct the cooling air where it is required
- sheet metal cover over the barrel to add extra protection and exhaust heated air
Extruder Base includes:
- heavy duty formed steel base with extensive cross-bracing to provide a vibration-free platform
- front barrel support to allow thermal barrel expansion
Manual Screenchanger
- Manually operated screen changer with pressure activated seal, easy access service and a multi-position handle. The extruder screw can be removed without removing the screen changer. Requires one heat control zone. Screens are not included.
Electrical control panel includes:
- Syscon – RKC REX C-400 self-tuning controllers with digital ammeters and heater break alarm. Three modes of control for the barrel zones, two modes of control for all other zones.
- drive controls with stop/start, speed potentiometer, digital screw RPM and load meters.
- melt temperature and pressure readouts
- required switches, solid state contactors, fuses or circuit breakers and wiring to numbered terminal strips
- Zone distribution:
- 5 heat/cool extruder zones
- 1 heat only screen changer
- 1 heat only primary extruder adapter
- 1 heat only custom distribution block
- 2 heat only zones in the downstream secondary adapters
- 2 heat only zones in each of the dies
Safety features include:
- overpressure release rupture disk, rated at 8500 psi
- finger guards on feed throat screw access opening
- cold start protection to prevent extruder drive from starting unless all heat zones maintain setpoint for a period of one hour
- AC drive to provide overload protection of the motor
- electrical components that meet CSA, UL or CE standards
- warning labels where appropriate for hot surfaces, pinch points and other hazards
Extruder Specifications:
Screw Diameter 3"
L/D 30:1
Barrel Zones 5
RPM 80
GEARBOX
L-10 Rating 265,276
HP Rating 198 hp
Drive HP 75hp
Specifications
Manufacturer | Brampton Engineering |
Model | 3" extruder |
Year | 2005 |
Condition | Used |